Outbound Logistics: What It Is & How to Do It Right
by
Yulia Miashkova
October 04, 2021
Logistics, quite literally, goes both ways. We could look at it from the point of last-mile delivery and say that there's shipping and then there's reverse logistics, i.e. returns. Logistics, therefore, covers going to and fro distribution centers and customers.
We could also characterize the two-way movement for logistics as inbound and outbound. One is all about the way raw materials and goods are moved to the company, and the other - about moving goods to the customer at home. As you can see, outbound logistics is last-mile delivery.
Today, we take a close look at outbound logistics to understand the network behind it, as well as how it compares to inbound logistics operations. Let's roll.
What is outbound logistics?
Outbound logistics refers to all logistics processes built for moving finished products from a storage facility to the end-user.
Outbound logistics includes the entirety of order fulfillment and serves the customer in every way it can - from shipping channels to packing, live tracking, and notifications.
When we talk about the 6 functions of logistics, we essentially talk about every outbound logistics process that supports the distribution network and the movement of finished goods to the customer.
Inventory, warehouse, picking and packing, and, of course, transportation itself. All of these are the steps of the movement of goods, and all of these create an outbound logistics network that can be established within a company or outsourced to a 3PL aka third-party logistics provider company.
Inbound and outbound logistics
Inbound logistics, on the other hand, encompasses all the logistical processes that have to do with moving raw materials into the company.
Essentially, inbound logistics is all about supply, suppliers, and supplier relationship management, which involves a lot of transportation but never includes the end-user.
Businesses approach inbound logistics differently depending on their industry, production capacity, and many other factors. Some businesses outsource inbound logistics processes and some manage them in-house.
Ultimately, inbound logistics is meant to support the supply chain with solid warehouse operations, storage, and inventory management. Depending on the demand for a specific product, businesses need to optimize their supply processes to cut operational costs and promote cost savings.
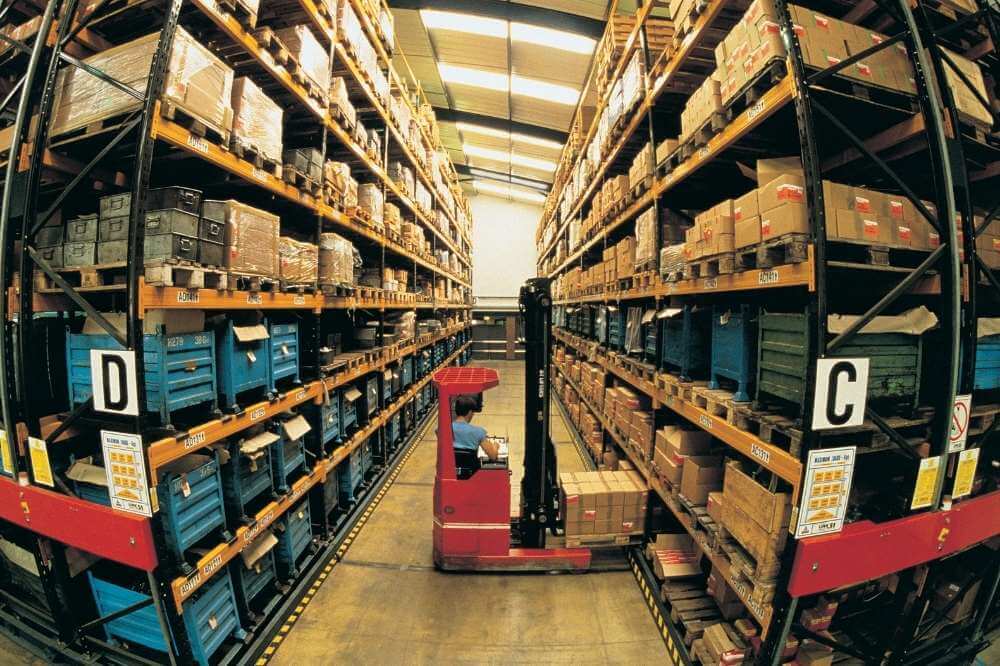
Inbound vs outbound logistics
When we talk about inbound and outbound logistics, we emphasize the difference between inbound and outbound processes, as well as the specific challenges companies face when optimizing their transportation operations.
Movement
First off, we need to talk about the difference in movement. While inbound logistics is concerned with getting raw materials into the company, outbound logistics is concerned with distribution, i.e. getting finished products to customers. Therefore, we can talk about inward vs outward movement.
Services
Second of all, the difference between inbound and outbound logistics is manifested through relationships with different shipping and delivery parties. Inbound logistics is concerned with supply and suppliers. The services that support inbound logistics supply management are B2B deliveries.
Outbound logistics is all about customers and efficient shipments, which includes real-time tracking, delivery updates, and other services that support customer centricity and promote retention and loyalty. Outbound logistics can be both B2B (wholesale) and B2C (home deliveries).
Supply chain
Both inbound and outbound logistics play their respective vital roles in the supply chain. While outbound logistics is built into the distribution network, it can be outsourced to a third-party logistics company (3PL). This is what many e-commerce businesses that can't afford a self-delivery system do.
Inbound logistics can also be outsourced, except outbound processes require 4PLs aka fourth-party logistics companies that manage not only the distribution network but also the entire supply chain, which includes suppliers and any 3PL partners involved.
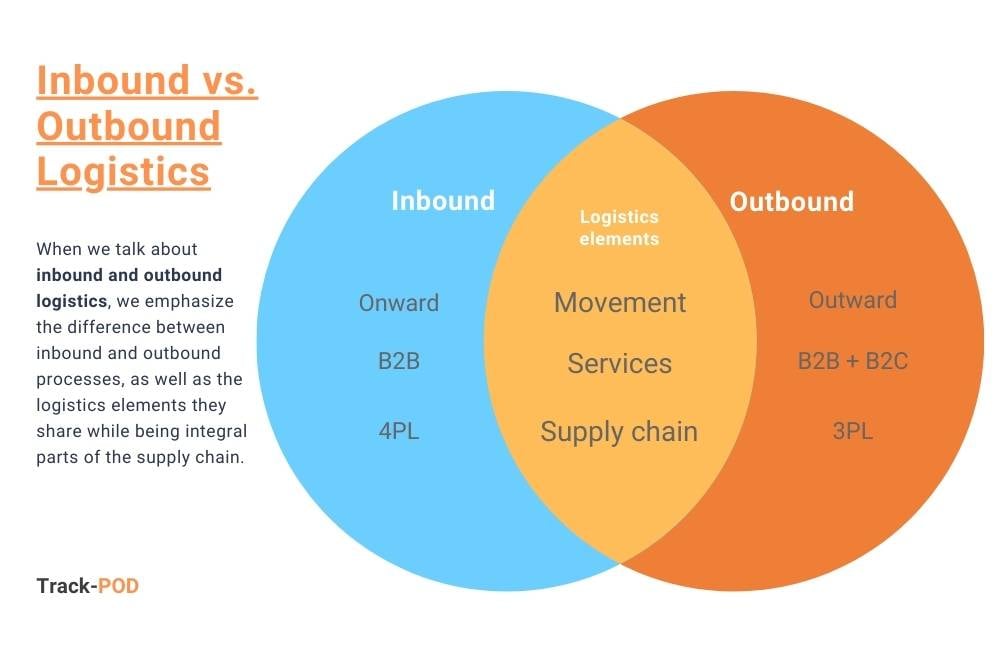
Examples of outbound logistics
Now that we've sorted out the definitions and outlined the difference between inbound and outbound logistics, let's look at the actual activities behind each aspect of outbound logistics.
Fulfillment
Order fulfillment in e-commerce is something covered by outbound logistics processes. Starting with sales and order processing all the way to the warehouse, inventory management, and last-mile delivery. All of the steps that go into efficient delivery of products to customers go under the umbrella of order fulfillment.
E-commerce customer expectations are always on the rise, and businesses need to come up with order fulfillment practices that keep the end-user happy while promoting cost savings. An example of this would be paperless deliveries, i.e. when the movement of goods is fast and efficient thanks to digital Proof of Delivery (POD) and instant communication with customers.
Shipping
Shipping is a key order fulfillment process that determines a big chunk of customer satisfaction. When we talk about shipping, we refer to the larger logistics network and all operations that support deliveries and delivery channels.
For a business whose distribution system relies on multiple inventory, warehouse, and distribution centers, outbound logistics processes need to align in order to meet the demand for finished products and match customer expectations in terms of delivery channels and related services.
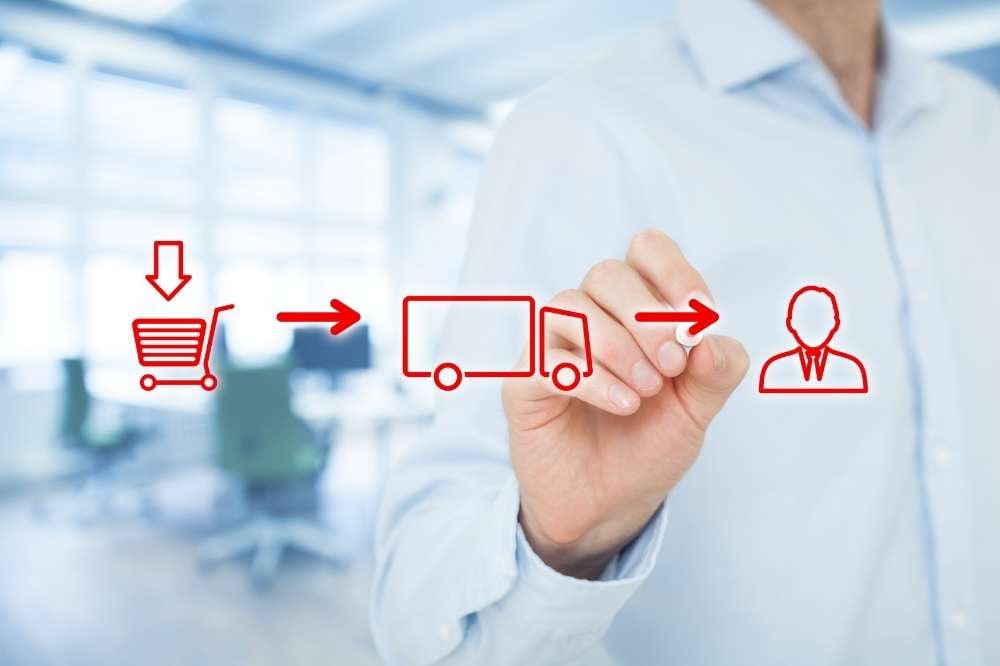
For example, a delivery management system like Track-POD is a software solution that businesses deploy for organizing inbound and outbound logistics processes that involve numerous suppliers, warehouse and storage locations, etc.
A delivery management system like Track-POD can plan and optimize every inbound logistics and outbound logistics process by building fast, safe, and efficient routes with multiple depots involved. This way, your business can focus on growing sales as your inbound logistics and route planning are covered.
Last-mile delivery
While the shipping strategy can be defined as the transportation strategy, which means a larger network that supports deliveries and pickups, the last-mile delivery strategy is the final steps of the outbound logistics processes in the supply chain.
Last-mile covers every logistics process that occurs in the final stages of distribution to the end-user: route planning and route optimization, fleet management, real-time vehicle tracking, and, of course, Proof of Delivery.
Outbound logistics covers all of the last-mile processes, and businesses handle those with the help of last-mile delivery software like Track-POD. From planning shipments from multiple warehouse and storage facilities to sending real-time delivery notifications to customers - a last-mile tool is deployed to automate and optimize the final stages of distribution.
Customer service
Speaking of real-time delivery notifications and live tracking, outbound logistics must serve customers first and foremost, and the larger business as an extension of that. Every outbound logistics process needs to be customer-centric because the success of distribution is determined by how quickly and efficiently finished products get to the customers.
Since inbound and outbound logistics rely on software and tools that support automation, the business costs of being customer-centric can be kept low while customer satisfaction remains high. Automated delivery notifications is an example of a service any business can adopt with minimal involvement of IT personnel.
Customer centricity is beneficial at every step of the supply chain but outbound logistics is where it brings the most value to the business.
Outbound logistics challenges and solutions
Now that we've talked about inbound and outbound logistics in the context of customer delivery, as well as the examples of outbound logistics services, let's take a look at the common challenges related to outbound logistics. Naturally, we'll also discuss some of the most popular solutions used by businesses doing inbound and outbound logistics.
Coordination
Inbound and outbound logistics both call for the smooth coordination of the entire logistics network. Raw materials handling and transportation to the production facility, inventory management, warehouse and distribution processes, as well as delivery to customers all require a lot of operational effort to keep suppliers, 3PL and 4PL companies, own resources, and customers in complete sync.
When we look at the challenges related to outbound logistics in particular, we need to consider the costs of inventory management and distribution systems that need to be integrated for the business to keep providing excellent service.
While some companies deploy tools and processes that support fluctuating sales and demand with services like same-day delivery, other businesses look for ways to cut warehouse and inventory costs.
Another popular solution that brings a lot of value to delivery companies is self-service for suppliers - an example of that could be a Customer Portal that suppliers can log in to manage and optimize their shipments independently.
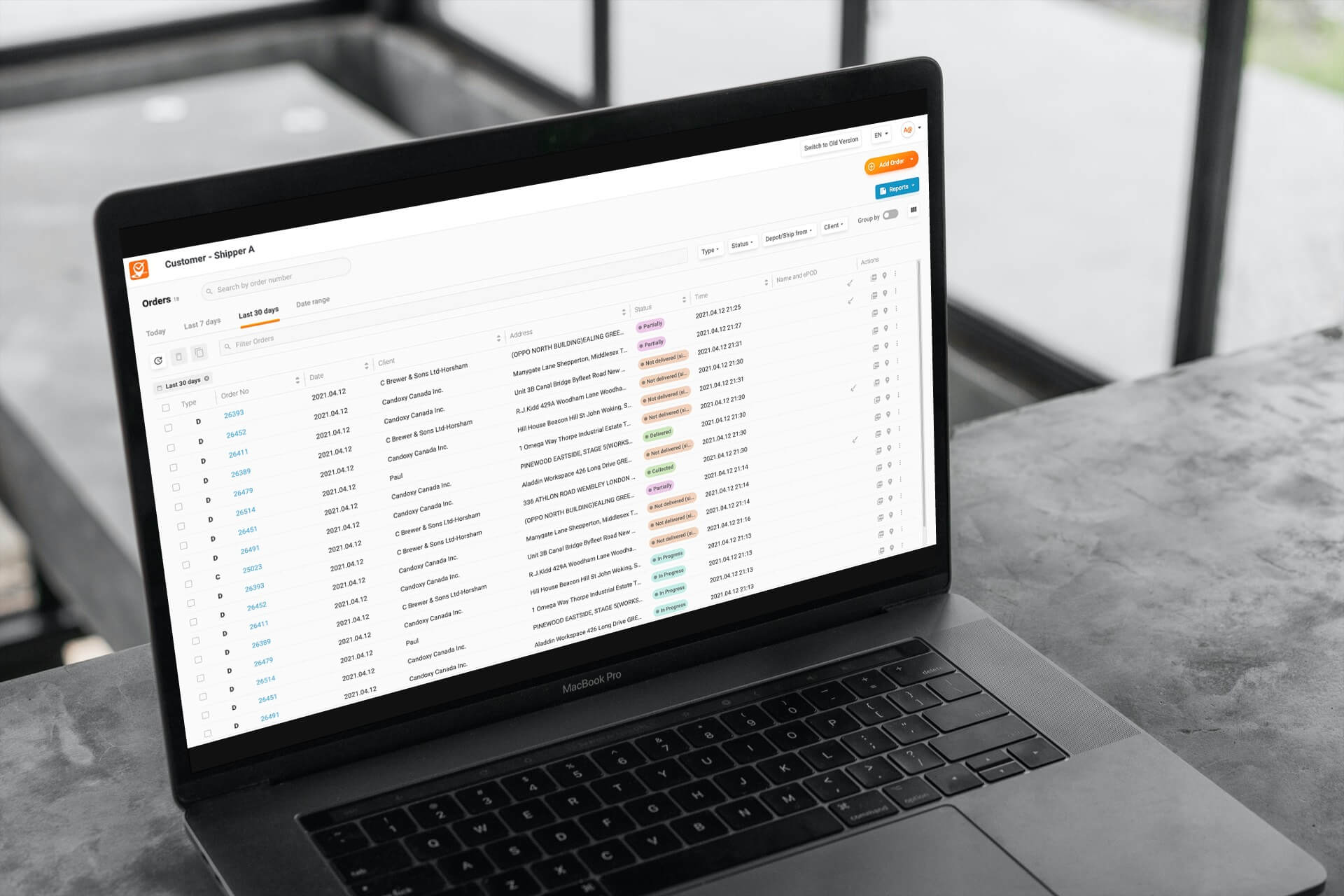
Logistics costs
Building an inbound or outbound logistics network comes with the need to be cost-efficient in order to keep bringing value to the business and customers alike. In addition to the cost of the production, inventory, warehouse, and distribution coordination, there's the ever-rising cost of transportation itself.
A sure-fire solution to minimizing logistics costs is a transportation management system (TMS) like Track-POD. A TMS is packed with solutions such as automated route optimization that makes the most of your vehicle space, supports fuel management for lower costs, and builds the fastest routes to minimize the working time of your drivers.
In addition to all of these cost-cutting measures, you get logistics analytics with actionable business insights. Whether it's the overall inbound logistics performance or insights into individual delivery drivers, you get a full overview of your every logistics process.
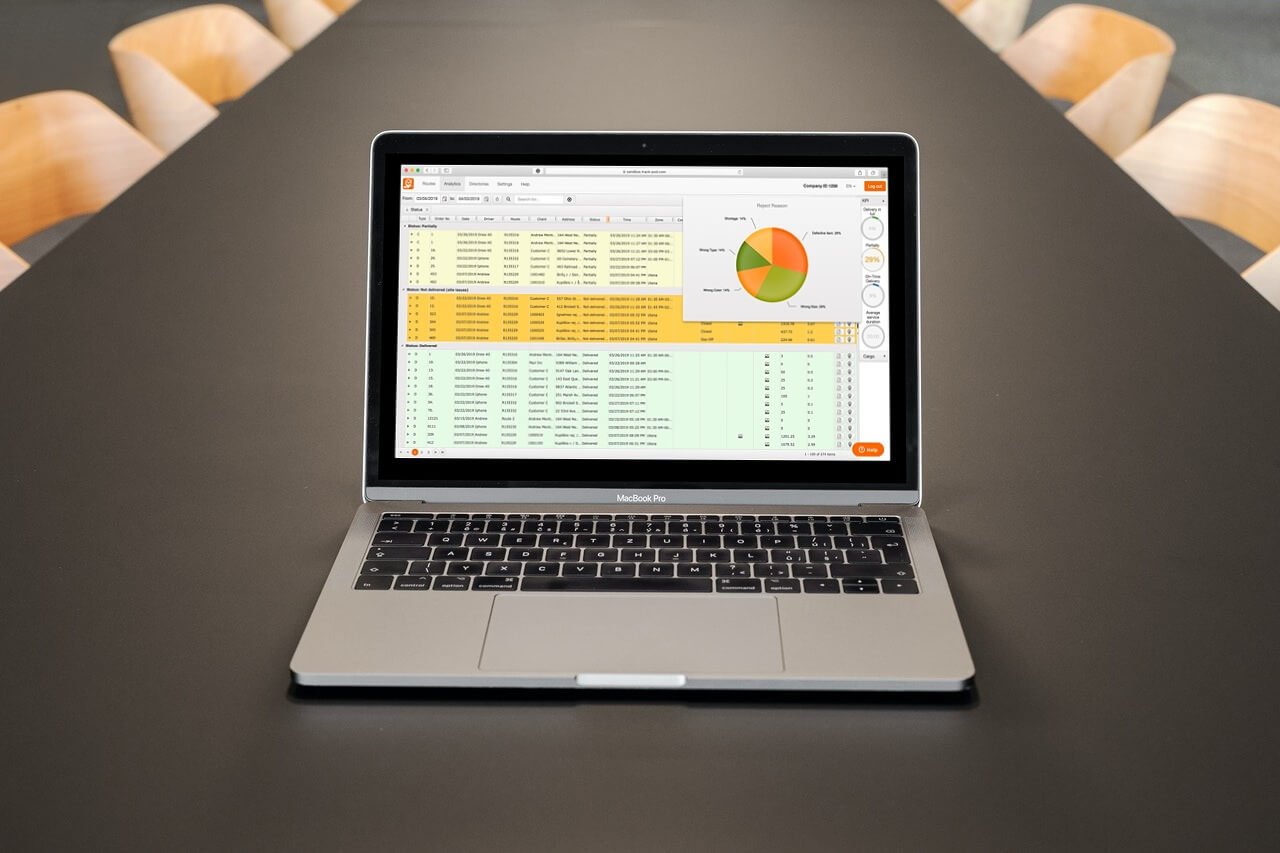
Customer expectations
We've talked a lot about customer service in this post. That's because outbound logistics serves customers and, therefore, needs to be customer-centric in every regard.
Big companies and small businesses alike are under great scrutiny today. The entire production, inventory, and logistics network has to meet certain customer demands like sustainable packing, flexible and free delivery, as well as the option to return and recycle products, which needs to be supported by a solid reverse logistics network.
Logistics - outbound and inbound - relies on customer-centric tools like Track-POD that work for the business but ensure top quality of customer service. From same-day, and contactless delivery to free returns and live courier tracking - your company has all the tools to optimize every logistics process and up the quality of your logistics service.
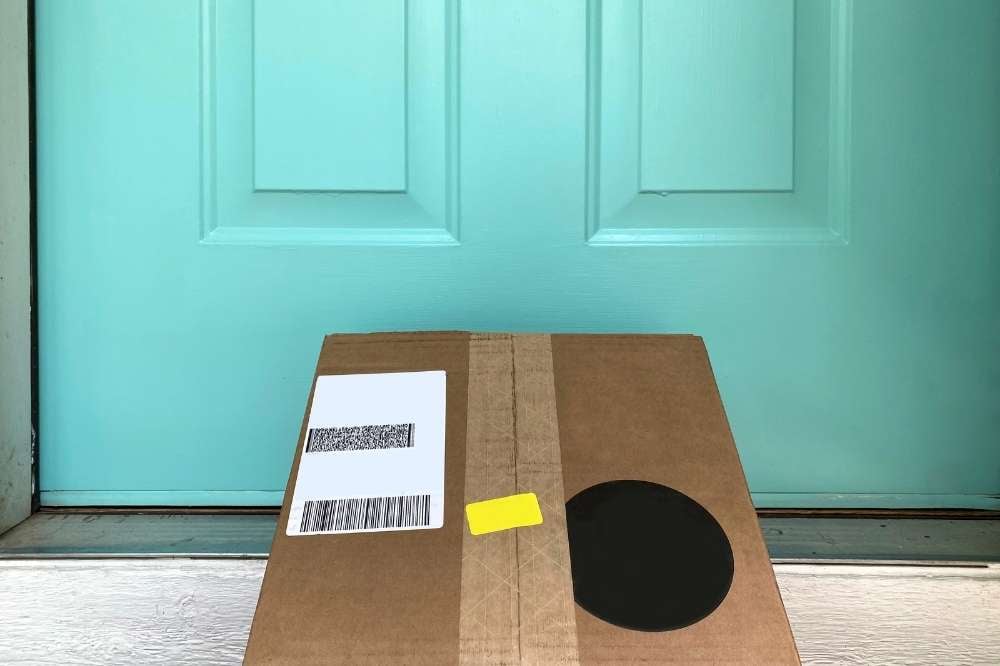
Recap
Inbound logistics and outbound logistics constitute the backbone of a company's production, distribution, and supply chain management at large.
Inbound logistics cover the movement of raw materials, supplier management, as well as inventory and warehouse management - all to produce finished goods and deliver them to the business: a storage or distribution facility.
Outbound logistics, meanwhile, is everything that happens between the business' distribution centers and customers at home. Outbound covers all of last-mile logistics and answers the actual demand for finished goods and products.
To build an efficient outbound logistics strategy, a company needs to consider every process that helps to move the goods from the business to the final destination, i.e. the end-user. This is done with the right inventory and delivery management tools like Track-POD.
I hope this blog post gives you enough insights into outbound logistics processes in relation to inbound logistics and the larger supply chain. To get more information on Track-POD solutions to outbound logistics challenges, book a free demo and we'll give you a guided tour around all the automation solutions for your business.
- Transportation management
About The Author
Yulia Miashkova
Growth marketing manager with a background in public relations, SEO, social listening, and Account-Based Marketing.