Partial Shipment and Redelivery: How to Do It Right [Q&A]
by
Alisa Cvilij
June 26, 2024
Even if you're operating a well-oiled delivery machine, things don't always go as planned.
Mistakes and force majeure happen. Your job as a delivery manager is to find the least costly way to correct all shipping mistakes and make customers happy.
Partial shipment and redelivery are a problem-solution type of combo. This blog post answers every question about partial shipment management with a single delivery driver app.
Let's roll.
What does partially shipped mean?
What is a partial shipment?
Partial shipment is a term that can be applied to two types of delivery scenarios.
- First, we have shipments that are intended to be shipped in parts. In this scenario, a shipper and a buyer agree that goods will be transported not in a single batch but separately.
- The other scenario is one where an order was supposed to be delivered in full. As in the case above, there are individual items in the order - but the customer never agreed to receive them in part.
Instead, the customer expects delivery in full but can only accept a partial delivery because of certain issues with the goods.
In this scenario, the delivery driver returns some items to the depot and facilitates a return.
What does partially shipped mean?
This is a question that is often asked. Partially delivered or partially shipped simply means that some of the goods have been delivered, but not all. Why not?
In a logistics environment, the reasons are usually quite simple:
- Damaged goods.
- Goods returned because they were incorrect.
- Goods were short-supplied, usually because there was not enough stock, but perhaps there was an error in picking or loading the stock.
But there are broader definitions. Partial shipments don’t always affect logistics operations.
Sometimes, customers want their stock delivered in batches, not all at once, because they don’t have space in their warehouse or shop. This has other implications because it costs the supplier to keep them.
If goods are still in the manufacturing process, the supplier may deliver the complete items in batches when they are finished.
Sometimes, big retailers require the stock to be delivered to different branches, which involves multiple deliveries. The order remains in a ‘partially delivered’ status on the customer’s account until everything has been delivered.
If a supplier does not have enough stock, the order will remain in a ‘partially delivered’ status until the stock becomes available. The order status will then change to ‘back-ordered,’ waiting for stock. Alternatively, the balance outstanding can be canceled, moving the order status from ‘partially delivered’ to ‘complete.’
Why do goods get rejected?
There are many reasons why customers reject goods. They may have been incorrectly manufactured, or the person picking the stock may have taken the wrong item off the shelf. The stock may also be damaged.
Sometimes, customers reject stock because the quality is not up to standard. Too much stock may have been supplied, and the customer will reject the excess quantity.
There are many reasons goods can be rejected in a delivery scenario. Generally, we can group the reasons for the rejection of items into two categories.
Wrong goods
Wrong goods refer to all cases where there has been a shipping mistake or a mistake in the production process.
In the case of a production mistake, the simple answer is to return the items to the manufacturer.
If it’s not a production error, shipping mistakes are the responsibility of the logistics operation and warehouse staff to sort out.
A loading mistake can happen if there's no load confirmation process in place. Drivers sometimes leave for customer sites with the wrong packages.
A solution to this would be shipping labels and a barcode scanner app. Drivers can use this to quickly check their loads and ensure that all loaded packages belong to the route.
Another reason for wrong goods is when the shipper packs the wrong size, color, quantity, or even the wrong product. Basically, it’s whatever the customer decides is wrong based on the mismatch between what they ordered and what they received.
Damaged goods
Damaged goods are a straightforward issue. Damage can happen even with careful load planning, when packages are loaded into the truck in a specific sequence determined by a smart system.
Loading needs to be planned based on package size, weight, etc., to avoid damage to the goods. Still, in force majeure cases, packages can be damaged, and the customer may reject some items in the order.
How do you document partial delivery?
Proof of delivery apps for the driver allows the user to collect customer e-signatures and take photos of delivered packages. By doing so, they prove the successful delivery of goods.
However, not all delivery driver apps account for scenarios where some items in the order have been delivered and others have not.
To document this, Proof of Delivery apps like Track-POD's driver app support Partial Delivery and Reasons for Rejection.
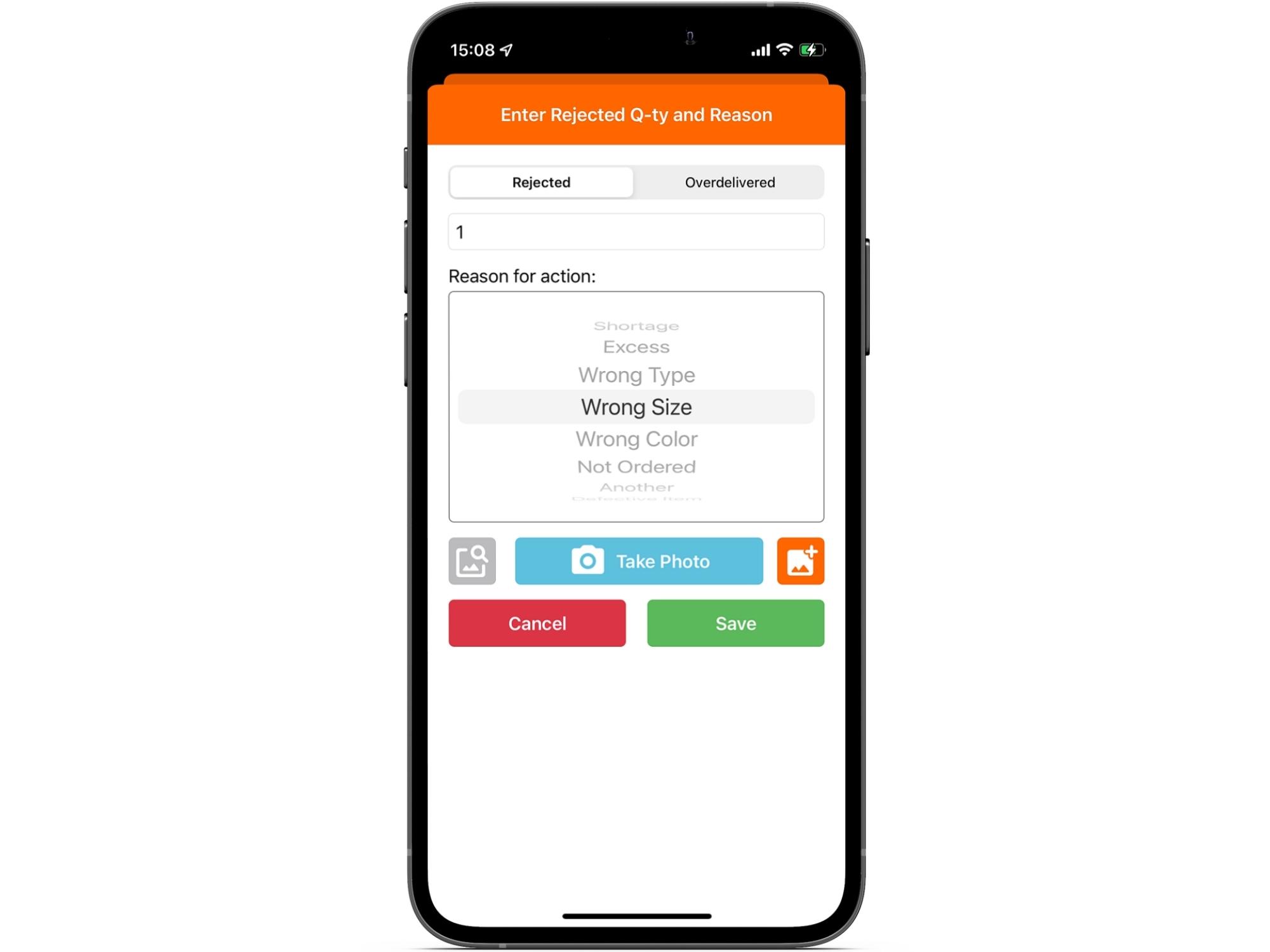
Pro tip: In case a driver over-delivered an order, i.e., brought more items than what was agreed upon, they can use the Track-POD app to document that as well.
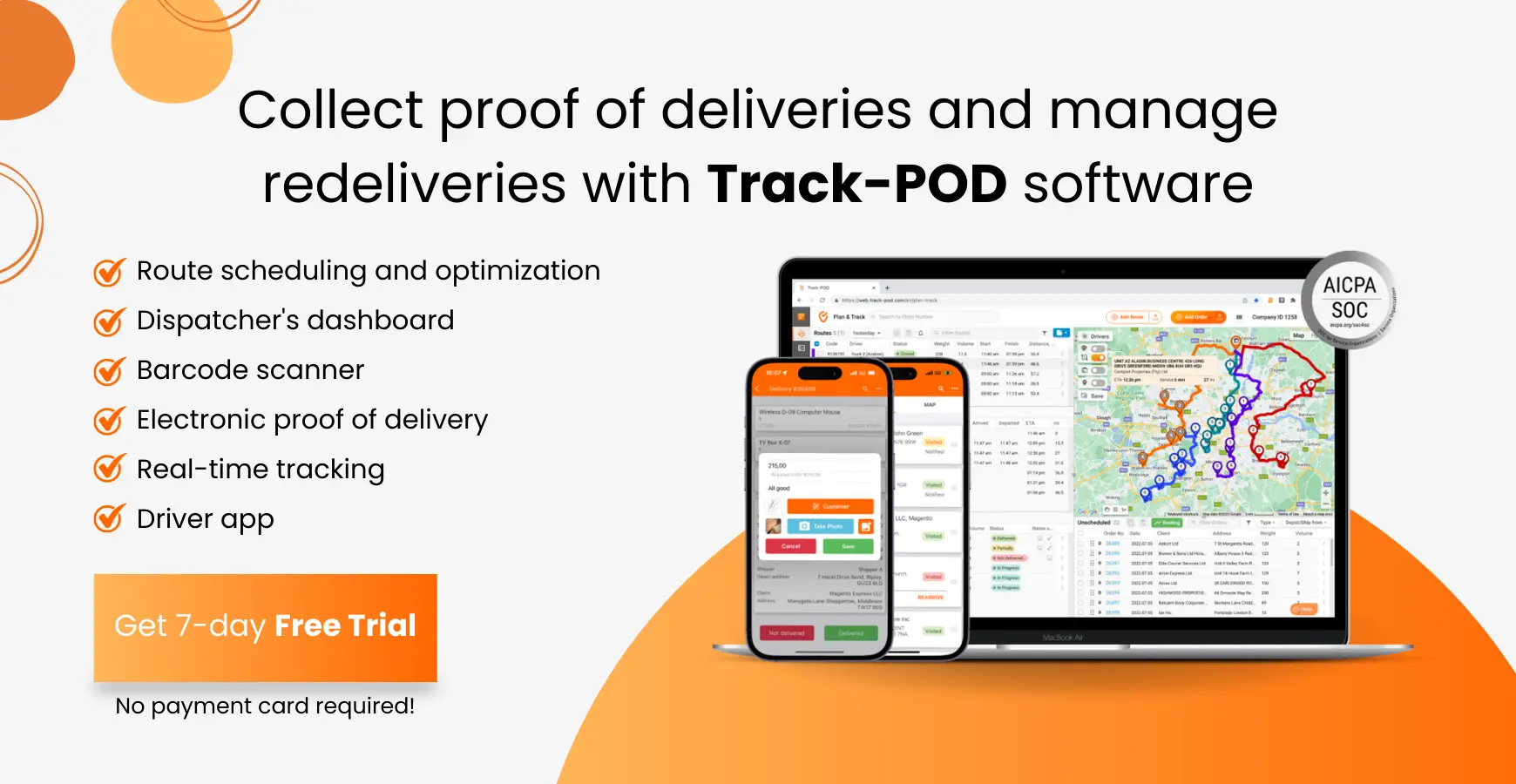
What is redelivery?
What do you do with a partial shipment to ensure a good customer experience? You go back to the depot or store location, retrieve the correct/undamaged items, and go back to the customer location.
This is what redelivering shipment is all about.
The higher the pricing point of your products, the more expensive it is to redeliver them. Likewise, the longer the journey your driver needs to make, the harder it becomes to redeliver.
What are the reasons for redelivery?
Partial shipment is not the only reason for re-delivery. Sometimes, a delivery job is unsuccessful for a number of reasons outside of your drivers' control.
Delivery driver apps like Track-PODs can account for different unsuccessful delivery scenarios. These may include a wrong address, a day off, the recipient not being around, etc.
Pro tip: Track-POD delivery software allows you to customize the reasons for delivery failure. This applies to both the rejection of individual items and why the delivery/collection failed.
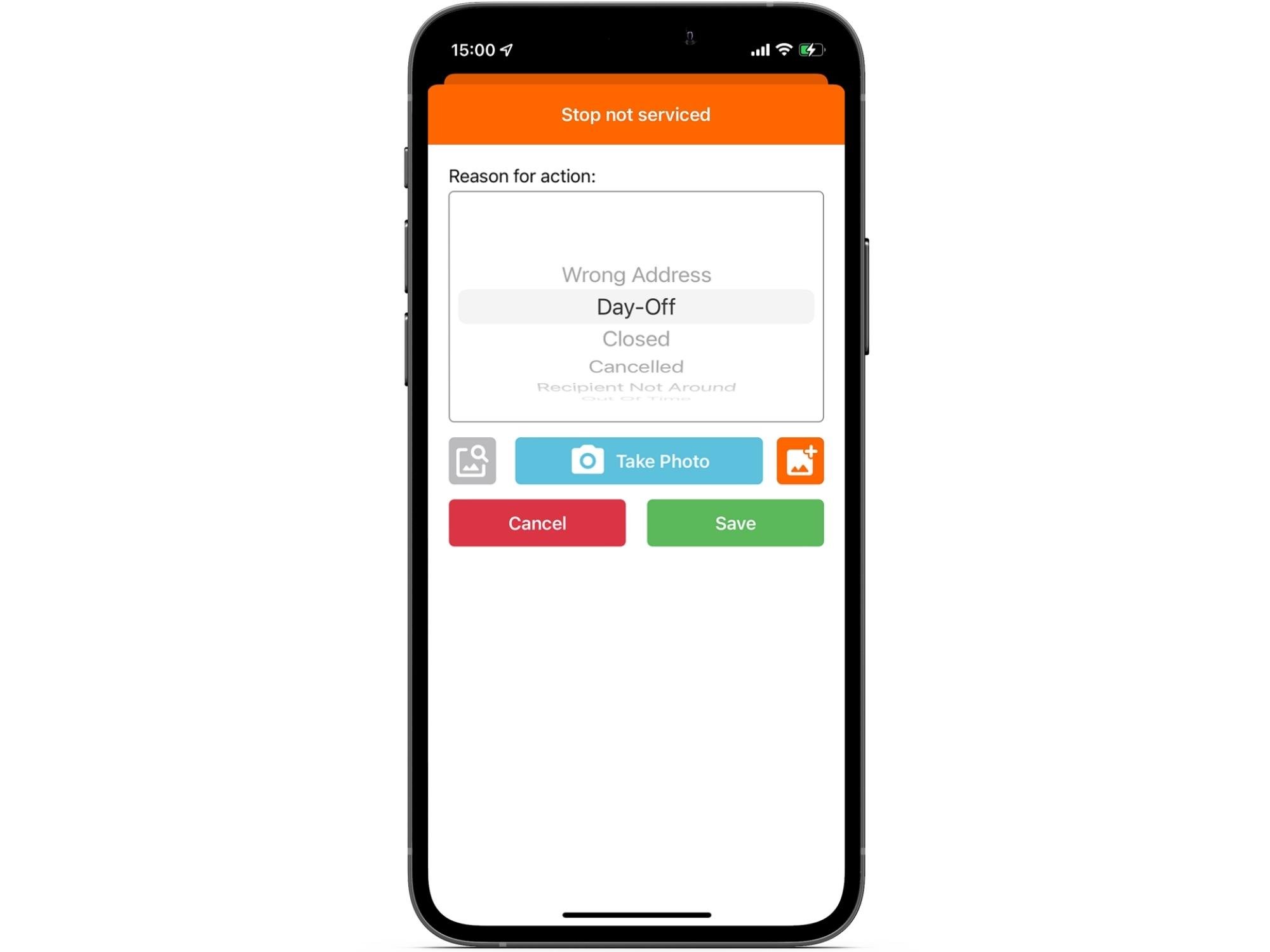
Pro tip: Track-POD delivery software allows you to customize both the reasons individual items are rejected and the reasons the delivery/collection has failed.
How to manage redelivery?
Redelivery is unfortunate as it will affect you in terms of time wasted and costs.
- Ideally, you should try to schedule it as part of a normal delivery route. This may be practical when your customer receives stock regularly, and they are happy to wait until the next delivery happens. Or you may be lucky enough to add it to a route that bypasses that location anyway. But this may not always be the case. If the customer cannot wait, it means the whole delivery process must be repeated. Only this time will you have to absorb the delivery costs. These include Dispatcher/route manager time.
- Driver time.
- Fuel costs.
The Track-POD driver app offers the Rearrive feature to save you time on route planning. By clicking on ‘rearrive, ' the driver can manage the redelivery independently of the other deliveries in the route plan.
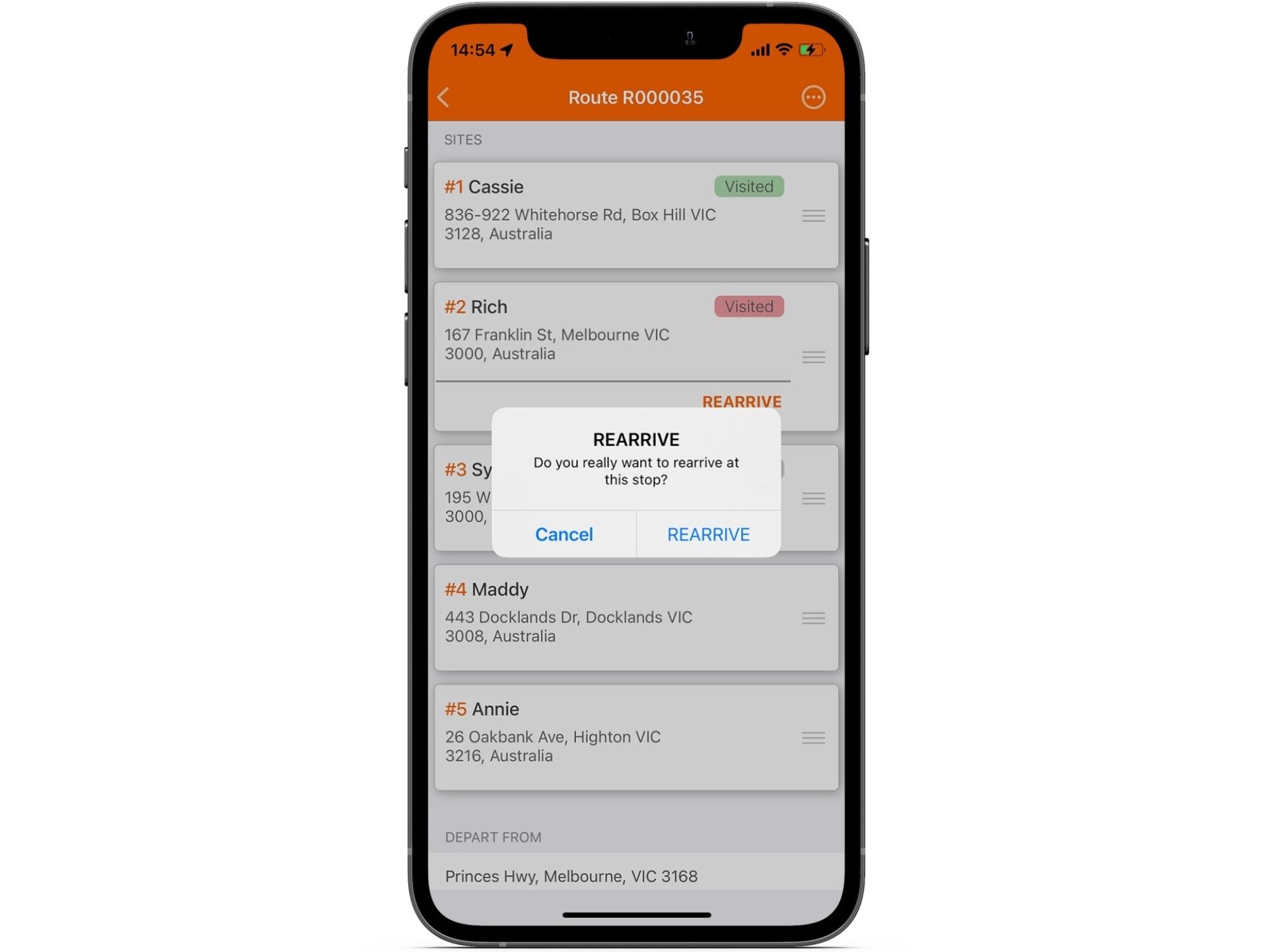
This is not always doable, as sometimes retrieving the correct items takes time. In this case, route planning can still be simplified by treating redelivery as a milk run on the app
A milk run is essentially a route you repeat regularly.
In Track-POD, a dispatcher can quickly duplicate or repeat an unsuccessful route. This way, you skip setting up a task from scratch. See the example below. (Mouse click on the route's setting - then select "Repeat")
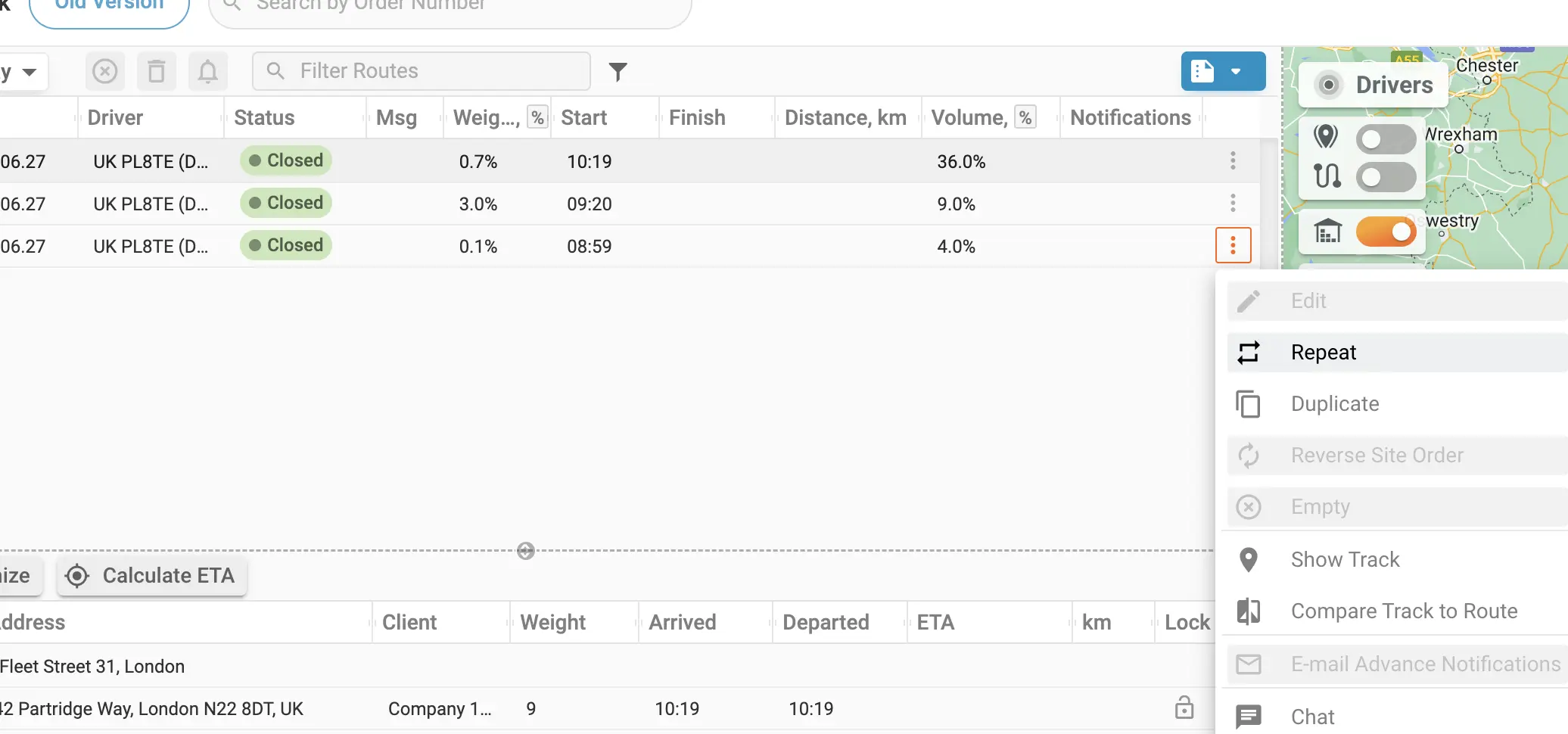
What are common reasons for redelivery?
Deliveries are often unsuccessful because of incorrect address details or because the customer is not around to receive them. It always helps to confirm the address and time of delivery with the customer before leaving the warehouse.
Track-POD’s software allows customers to track their delivery and be available to receive it. Incorrect addressing is a result of human error. People capturing orders should verify the details. It helps to send the customer an email notification of the ETA with the address included. That way, any inconsistencies in the address can be picked up and fixed.
Another common problem with deliveries is damaged goods. Suppliers and logistics organizations care for their packaging, but some goods are fragile or perishable. Proper marking in these cases helps prevent damage. Large FRAGILE stickers or bright red adhesive labels will alert packers to the packages' fragile nature.
Recap
Partial shipment and redelivery are both delivery scenarios most businesses would like to avoid altogether. And while there are many precautions you can take to minimize your rate of partial or unsuccessful deliveries, things can still go wrong.
What's important is that you have all the know-how and tools to document partial shipment cases and organize redelivery as cost-efficiently and possible.
If you're curious about Track-POD solutions to partial delivery and redelivery, book a free demo and let's talk.
About The Author
Alisa Cvilij
Content Marketer at Track-POD. Passionate about building meaningful and helpful content for the readers.